This story appears in the April issue of Utah Business. Subscribe here.
Last month, Utah Business partnered with Foley & Lardner to host a roundtable on Utah’s manufacturing industry. Moderated by Tulinda Larsen, president of the Utah Advanced Materials Manufacturing Initiative (UAMMI), they discussed Industry 4.0, sustainability, reshoring and more.
How does your company define advanced manufacturing and Industry 4.0?
Win Jeanfreau | Executive Director | iMpact Utah
Automation comes to mind, but it’s really the fourth generation of manufacturing where you’ve got a combination of organic and mechanical. It’s when a full variety of components come together under an infrastructure that allows the industry to be more responsive to demand. It allows the human to do the human component really well and the automation portion to do the repetitive, hot and dangerous work. Industry 4.0 is that new blend of digital solutions with an organic component. The challenge is maximizing training and education for the human element of that process.
Todd Bingham | CEO & President | Utah Manufacturers Association
Not only is it robotics and automation, but it’s also the monitoring of stress, temperatures and equipment. When we talk about Industry 4.0, it naturally takes me into artificial intelligence (AI). Manufacturing is so intrigued by AI because it means continuous improvement. But is the juice worth the squeeze? What will it cost to invest in AI, and what returns do you get in terms of data? That’s different for every company.
Jason Meredith | VP | Northrop Grumman
When you look at aerospace and defense, our customers still struggle with evolving. Are all of us using manufacturing 4.0? Yes, but we have to match the speed at which the Department of Defense is moving. They are not at a place where they would allow continuous improvement of the process. Our customers, like the Department of Defense or NASA, are very interested in ensuring we make a part precisely the same way we made the last part. As we move forward, the markets we’re addressing will have different response rates.
Marshall Hagen | Senior Manager, Strategic Growth | Janicki
Chairman | UAMMI
Janicki has used AI to compensate our 100-foot-long 5-axis machines for over 10 years. AI is a new phrase for complex algorithms and systems that input and output data. We look at AI today like people thought about automation five years ago. Everyone thought automation would drive the labor out of the workforce and revolutionize everything, but it improved the capability of the supply base.
Nathan Imfeld | Senior Counsel | Foley & Lardner
Our clients are seeing and struggling with a lot of the same things. Any government contractor, whether with the Department of Defense or any other government agency, deals with a regulatory regime that changes very slowly, if ever. They have to adapt their manufacturing processes to account for that. This means that the focus — if you’re talking about advanced manufacturing or Industry 4.0 — is more around saving labor than anything else.
What are the new opportunities your company would like to pursue?
Jeff Young | EVP | YESCO
We’re pursuing automated processes for sign creation. Our challenge is that different cities’ codes require us to maintain signs of different sizes. As customers want to maximize their sign sizes, each sign we make is new — even if we’ve created a similar one before. Our other challenge is that we can’t build signs without permits, and we can’t get permits because no one works in office post-COVID-19. We wait weeks and sometimes months; we can build signs faster than we get a permit.
Johnny Ferry | VP, Business Development | Honeyville, Inc.
Everybody has had to eat. Ours is a very basic industry in this way. But the next level for us continues to be data mining. We want a formula that mixes the perfect amounts of sugar, flour and other ingredients to make the perfect cookie and frosting. If we use AI, it can draw upon countless amounts of data to create the perfect cookie for each person based on their palette. That’s the kind of technology we’re starting to get into — more focused on the individual.
Matt Sterbenz | GM, Wintersports | Checkerspot, Inc.
While AI can play a part in data mining and help us develop smarter and more clever materials, the materials are the innovative story. Our audience is desperate for innovation and transparency. We must challenge those decade-old manufacturing processes and use renewable materials that don’t sacrifice performance for sustainability. We come to the table not offering automations but unique material applications.
Jennifer Hwu | CEO & President | Innosys Inc.
We are heavily involved in research and development. We are constantly researching and developing product lines. Recently, we started to manufacture additive ceramics. It’s unique and doing well. Now, we are evaluating the metal additive in manufacturing. Those are the two big material systems we use.
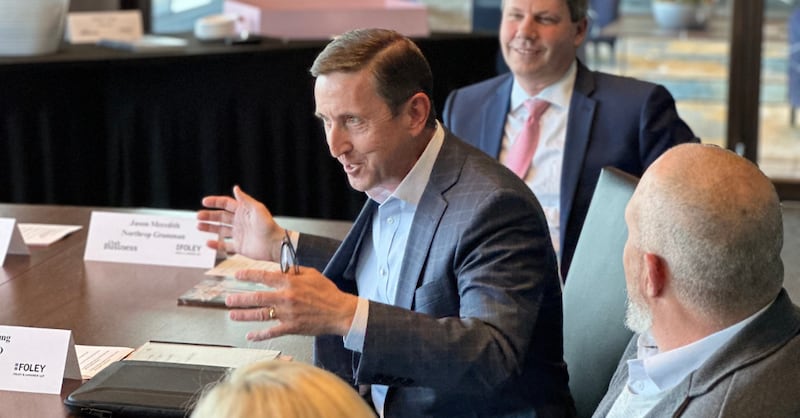
What can manufacturing do to be more sustainable?
Spencer Loveless | Founder & CEO | Merit3D
CEO | Dustless Technologies
We just got an order from one of the largest cellphone companies in the world, and their initial question was, “How is this sustainable?” All these big companies want to reduce their carbon footprint and do their part for the planet. We have the blessing and the curse of being involved in material development where we can drive what our customers want: bio-based, recyclable, sustainable. As manufacturers, it’s driven by the companies as our consumers.
Jason Meredith | VP | Northrop Grumman
Sustainability is a huge priority. Our CEO, Kathy Warden, has spoken a lot about it and has established goals for us to drive improved sustainability. We’re looking at all kinds of ways we can drive sustainability within our processes. Oftentimes, when you look at Northrop Grumman, you don’t think “green,” and you certainly don’t think “sustainability.” But we’re looking at ways to drive down greenhouse gases from our applications and investing large sums of money into driving down our footprint.
Nathan Rich | Founder & CEO | IsoTruss, Inc.
We just returned from Paris, the JEC show, and there’s a big disconnect here. There are a lot of government institutions or companies that say that they want to be sustainable and move things forward, but when you get into the organization and talk to procurement, those same decisions don’t flow through. A lot of responsibility is on us as consumers to make more sustainable decisions and have a bigger impact. The driving factor in the decision is the actual price of the product. Europe is further ahead in sustainability than we are here in the United States, and they take it a little bit more seriously.
Win Jeanfreau | Executive Director | iMpact Utah
A ton of research has been done on consumer behavior. Surveyed consumers say they want green, sustainable businesses, but they struggle to define what that is. Then, if you look at their behavior, they buy everything on Amazon and burn the boxes. As private consumers, even those who profess a political flag in the ground still behave with disregard for the carbon footprint of their choices. The industry will get green when it makes financial sense for the industry to get green. As industry leaders, we must show how it benefits the bottom line. There are ways to do that without embracing philosophies that can’t be sustained financially.
Johnny Ferry | VP, Business Development | Honeyville, Inc.
In food manufacturing, there are two areas of sustainability: food waste and packaging waste. There’s more than enough food to feed the world, but getting it to the consumer is a challenge. For packaging, we’ll produce 500 million pounds of product this year and every pound of that moves in some form of a package. Most of it ends up in the waste, particularly in areas where we don’t have recycling programs. We can help by making the packages biodegradable. As individual consumers, we all have a choice to make when we pick up a product and decide to buy it. We have to continue to push the message that those choices impact how we will live in future generations.
Marshall Hagen | Senior Manager, Strategic Growth | Janicki
Chairman | UAMMI
Our manufacturing sites are often built to print or already designed, so we are constrained in the materials we’re using to build the products. One of the gaps discussed in the past is how to deal with recycling pure composite materials. There are government restrictions on what we can do with the waste from the subtractive manufacturing processes. We need to figure out how to recycle, what a high-waste process or a subtractive process is, and obtain that waste reduction goal we should all strive for.
Matt Sterbenz | GM, Wintersports | Checkerspot, Inc.
A lot of the work we do is being thoughtful about the life cycle analysis of product and allowing there to be a seat in the room for that voice when making decisions. It takes discipline, but it leads to clever solutions. We work with an Ogden manufacturer named Origen, an expert in forged composites. We take that production waste stream and reintegrate it into future products. We’re alleviating the cost of landfill use and elevating performance with this new industrial aggregate that is a composition of our waste. We can reimagine the manufacturing process in many different ways if we open our minds to using a different suite of materials.
Jeff Young | EVP | YESCO
We have a lot of steel and aluminum in our process. As signs come down, recycling is pretty straightforward. We also recycle plastics and all of our lamps. We’re actively engaged and involved in retrofitting lighting systems everywhere to LED. All the old traditional lights in the Intermountain signs 20 years ago are now LED.
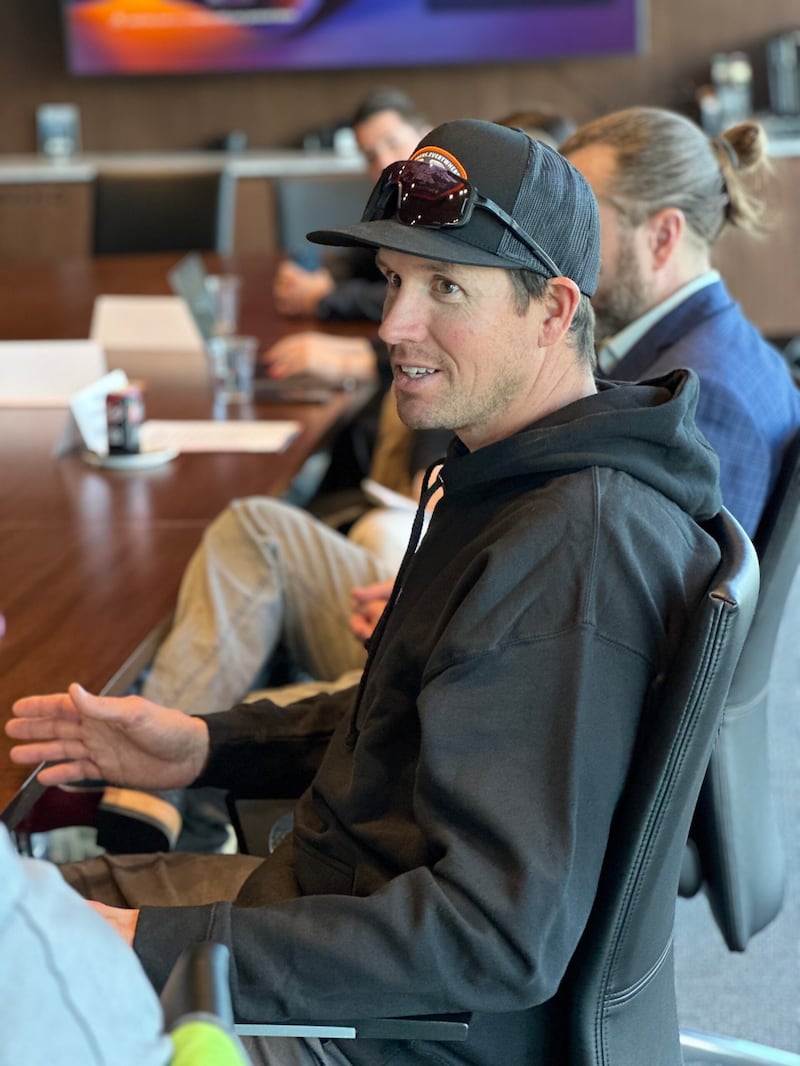
How do we support bringing manufacturing back to the United States?
Todd Bingham | CEO & President | Utah Manufacturers Association
We did have some companies that reshored steelwork into the U.S. but very quickly went back overseas. The only way we will see reshoring is with more efficiency, productivity and throughput. One of our companies said they needed to be at least three times more efficient than their facilities in Asia to manufacture here.
Nathan Imfeld | Senior Counsel | Foley & Lardner
The issue with reshoring is all regulatory. It’s tariffs; it’s trade compliance. One interesting thing I’ve heard a lot of manufacturers focus on is how to get the engineering design expertise close to the manufacturing and sell that as a package to your customers. You can add value to a product by giving customers access to the designers, builders and installers. Also, how much easier is it to go to a manufacturing facility just down the block?
What is the current state of Utah’s manufacturing industry from your perspective?
Spencer Loveless | Founder & CEO | Merit3D
CEO | Dustless Technologies
When we say we manufacture in mass by 3D printing parts, people think we are making 10 pieces. We’re making millions. But we have to engineer your parts so that they come out looking good. The manufacturing industry doesn’t know how to use the new technologies to design for the new processes that are coming out.
Jennifer Hwu | CEO & President | Innosys Inc.
Utah is a great place to do advanced manufacturing. I foresee advanced manufacturing growing quite a bit and quite fast in this state. I’d like to see the state continue to work on clean air and the water shortage. We are growing and expanding. I’d like not to worry about what happens if we don’t have enough water or clean air to support our future generation of employees.
Nathan Rich | Founder & CEO | IsoTruss, Inc.
The state of Utah is very open, enabling a cooperative and collaborative ecosystem for manufacturing currently trailing software and tech. Over the next decade, that trend will swing.
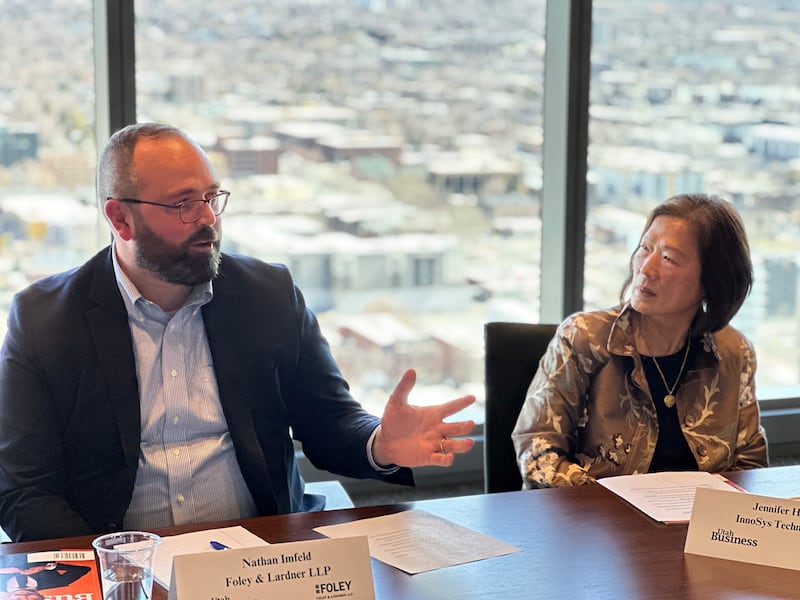